造成塑膠模具加工硬度不(bú)足、硬(yìng)度不均的原因是什麽?
模具熱處理硬度是非常重要的力學性能指標,硬度不(bú)合(hé)格(gé)是十(shí)分嚴重的缺陷。模具熱處理後硬度不足或硬度(dù)不均將使模具耐磨性及疲勞強(qiáng)度等(děng)性能降低,塑膠(jiāo)模具(jù)加(jiā)工廠家表示這將導致模具早起失(shī)效(xiào),嚴重降低模具的使用壽命。
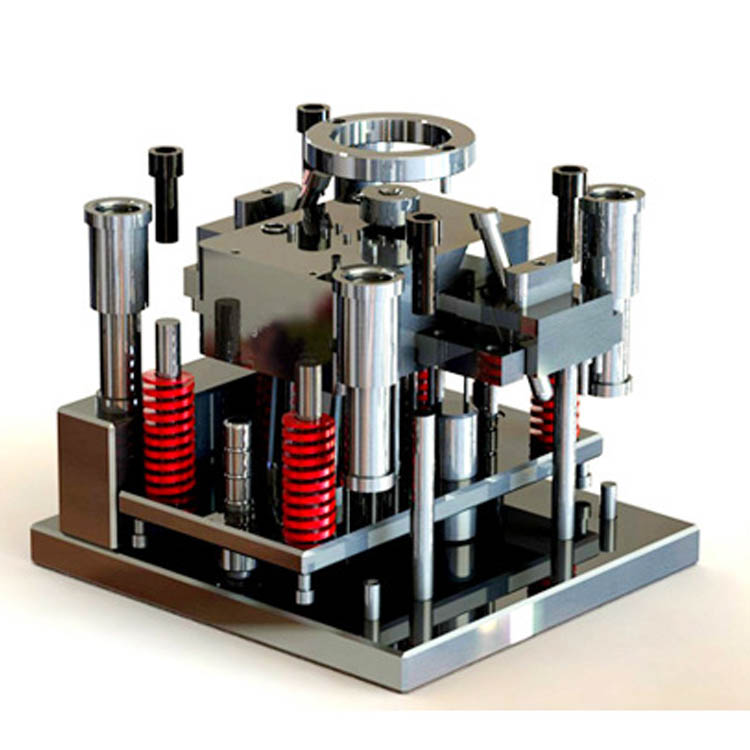
產生原(yuán)因:
1)模具(jù)截麵大,鋼材淬透性差,如大型模具選用了淬透性低的鋼種。
2)模具鋼(gāng)原始組織中碳化(huà)物偏析(xī)嚴重或組(zǔ)織粗大,鋼中存在石墨碳和碳化物偏(piān)析、聚(jù)集。
3)模具(jù)鍛造工藝不正確,鍛(duàn)造後未進行很好的球化退火,使模具鋼(gāng)球化組(zǔ)織不良。
4)塑(sù)膠模具加工表麵未除淨退火或淬火加熱時產生的脫碳層。
5)模具淬火(huǒ)溫度過高,淬火後殘留奧氏體量過多;或淬火溫度過低,加熱保溫時間不足,使模具鋼的相變不完全。
6)模(mó)具淬(cuì)火加熱後冷卻速度過慢,分級與等溫溫度過高或時間(jiān)過長(zhǎng),淬火冷卻介質選擇不當。
7)堿浴水分過少,或淬火冷卻介質中含雜質過多,或淬火冷卻介質老化。
8)模具淬火冷卻後出淬火冷卻介質時溫度(dù)過高(gāo),冷卻不足。
9)回火不充分及回火溫度過高等。
如果你想(xiǎng)知道更多關於塑膠模具加工的信息請關注: